
The Measure phase is where baselines are drawn to assess the performance of a given process.
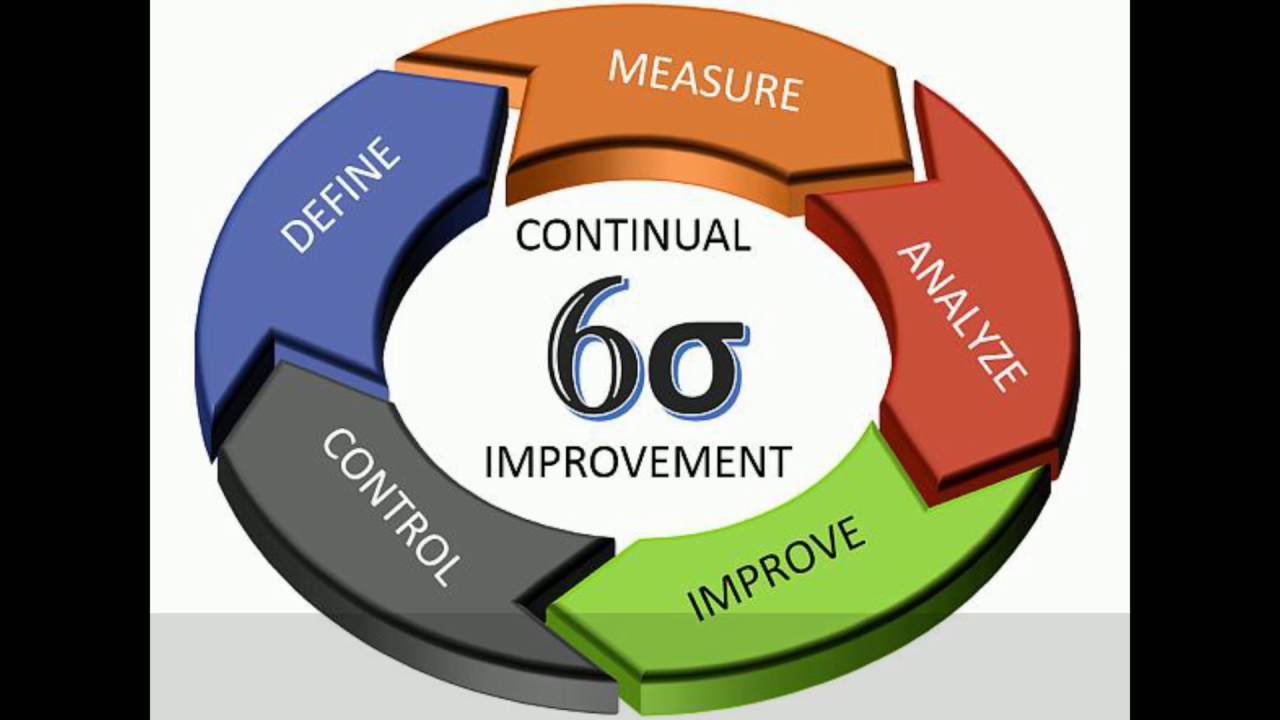
This phase is also about mapping the process, focus, scope, and the ultimate goal as well as understanding how the problem affects all stakeholders. Defineĭuring this phase, we select the most critical and impactful opportunities for improvement. The five phases (and an explanation of each) are: 1. The DMAIC process follows five key phases, which are intended to lay the groundwork for your process improvement, chart goals, track progress, and analyze results. The condition is assessable, and the outcomes can be understood appropriately through quantifiable means.Īfter you have evaluated the above factors, you can conclusively determine if your process can benefit from implementing DMAIC.There is potential to reduce variables such as lead times or other flaws while improving variables like productivity or cost savings.There are apparent inefficiencies and defects in the existing process.How do you evaluate those conditions? Here are three main factors to consider:

Recognizing the right conditions and choosing the right problem to solve are key to understanding whether DMAIC is the right tool for you. There are specific conditions where this technique can be the right fit for process improvement. The reason why this step is important, despite not being formally a part of DMAIC, is that DMAIC cannot be applied to all situations. Why the DMAIC Process?īefore we dive into the main process, there’s one additional step that some companies employ in order to figure out whether DMAIC is the right approach to solve their problems. You can read more about the history behind DMAIC and Six Sigma developments here. But the technique as we know it today has been shaped by some of the largest organizations in the world such as Toyota, Motorola, GE, and Ford Motor Company. Shewhart at Bell Laboratories in the 1930s. The DMAIC methodology has its roots in the PDSA (“plan, do, study, act”) cycle developed by statistician Walter A. The acronym stands for the five phases - Define, Measure, Analyze, Improve, and Control, and it is pronounced “duh-may-ik.” DMAIC is a data-driven problem-solving technique designed to identify and address inefficiencies in a process, which improves its outcomes and makes these improvements more predictable. While it’s associated with Six Sigma, this strategy can also be applied to lean and other process-improvement strategies.
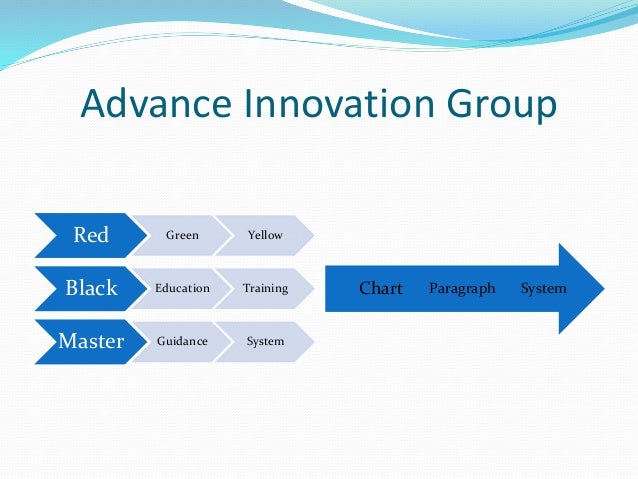
#6 sigma training software
When we look into the definition of DMAIC, it is a five-phase strategy for improving a wide variety of organizational processes, whether it’s software development, manufacturing, or some other process. A Six Sigma project is driven by the DMAIC improvement cycle.
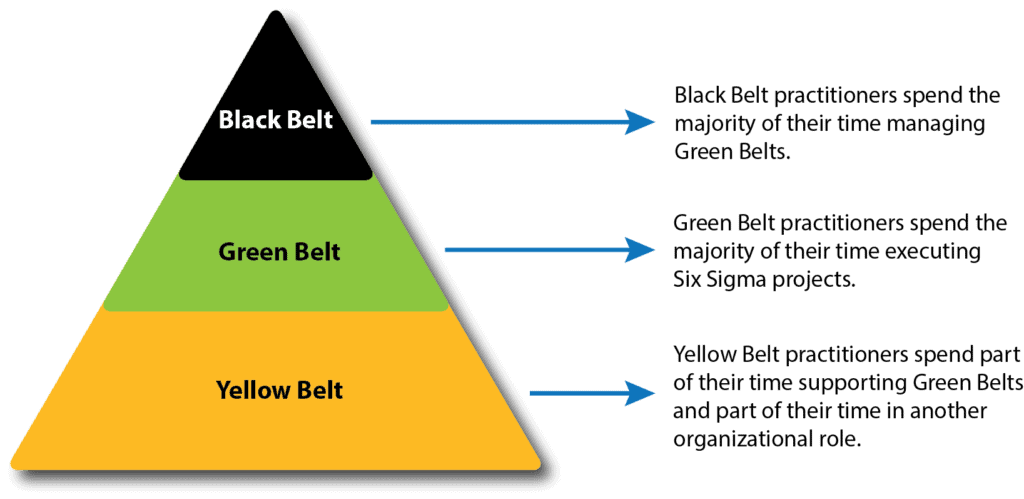
The process includes five phases: defining the problem, improving the activity, identifying the opportunities for improvement, setting project goals, and meeting the needs of the customer (internal and external).ĭMAIC refers to a cycle of process improvement that is data-driven and aims at improving, optimizing, and stabilizing business processes and designs. Enroll Now! What is DMAIC?ĭefine, Measure, Analyze, Improve, and Control is a DMAIC acronym. Get an overview of Six Sigma and the DMAIC methodology with the Lean Six Sigma Green Belt Certification course. With proper implementation of DMAIC, businesses have shown to benefit in several areas, including cutting down the cost of poor quality, boosting revenue, and improving business performance and productivity on the whole.
